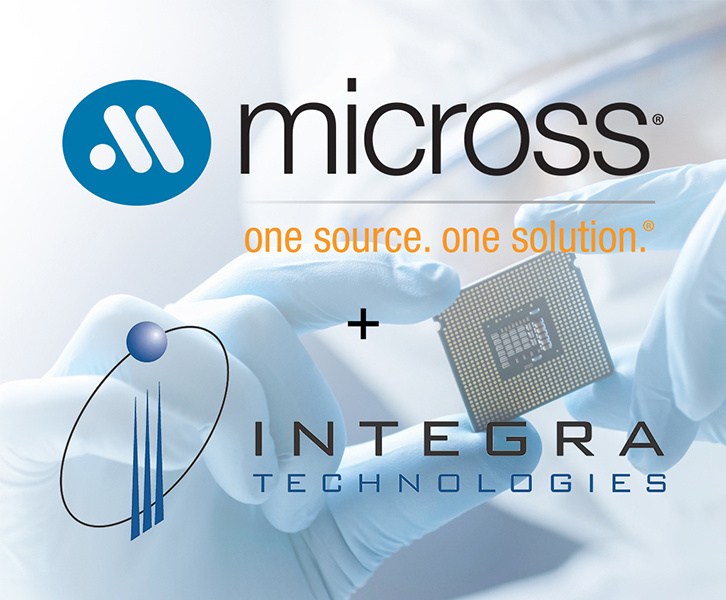
TOWA Compression Molding Unit Added
Integra Technologies is excited to announce the addition of a TOWA Compression Molding unit to their Silicon Valley facility. The unit
Laser Grooving Service
Integra Technologies is excited to announce the addition of Laser Grooving to their long line of product offerings
Supplier Excellence Award
Integra is proud to have been recognized by Northrop Grumman for our successful supplier partnership. Recognized for Quality Excellence,
Integra Selected to Participate with NCMS for Second Year
Integra Selected to Participate with NCMS on Developmental Program for Silicon Photonics
Brett Robinson, Wichita Business Journal Executive of the Year 2023
The Wichita Business Journal recognized Brett Robinson, CEO and President of Integra Technologies, Inc., as one of its 2023 Executives of
Integra Technologies Adds FC150 Automated Die / Flip Chip Bonder
With Heterogeneous Integration and finer flip chip pitches becoming a reality, Integra Technologies recently added a FC150 Automated
Integra Technologies on CNBC
Thank you CNBC for highlighting Integra on the one year anniversary of the CHIPS Act this month. We are thankful for the efforts of all our
Integra Technologies Adds Vice President of Quality
Integra Technologies is excited to have Don Warring join the Integra team as the Vice President of Quality. Don is an industry veteran
Integra Technologies Announces Site in Wichita Region
Integra Technologies Announces Site in Wichita Region for Largest U.S. OSAT Semiconductor Project Bel Aire, Wichita and Sedgwick
BREAKING: Integra Selects Kansas for Largest OSAT Semiconductor Project
Integra Technologies Selects Kansas for Largest OSAT Semiconductor Project Kansas State Finance Council’s APEX vote paves way for
ISO/IEC 17025:2017 Certificate of Accreditation
Integra Technologies recently received the ISO/IEC 17025:2017 Certificate of Accreditation from the ANSI National Accreditation Board for
Comprehensive Testing of Connectors
Integra Technologies offers a full range of Qualification, Design Verification, and Reliability Testing for the harsh environments required
Integra Expands Growing Line of Burn-in and Life Test Equipment
Integra Technologies is pleased to announce the addition of a Tahoe Burn-in System to meet the growing technical demand of burn-in and life
Integra and the Artemis Orion Spacecraft
Integra Technologies and the Artemis Orion Spacecraft
Integra's Albuquerque facility moving into Integra's Wichita facility
Dear Integra Technologies' DPA, Failure Analysis and Qualification Customers using Integra Albuquerque, NM facility -
Integra Completes Purchase of Presto Engineering's US Based Test Assets
Silicon Valley, CA, March 31, 2022: Integra Technologies is pleased to announce the completion of the purchase of Presto Engineering’s
INTEGRA TECHNOLOGIES SILICON VALLEY ADDS NEW FLIP CHIP BONDER
Silicon Valley, CA (Aug 18, 2021) - Integra Technologies, a world leader in semiconductor packaging, assembly, test, characterization,
PRESS: Integra Technologies Adds V93000 SmartScale Tester
INTEGRA TECHNOLOGIES ADDS V93000 SMARTSCALE TESTER The addition of this SmartScale Test system allows Integra to now support their
INTEGRA TECHNOLOGIES EXPANDS SILICON PHOTONICS CAPABILITIES
INTEGRA TECHNOLOGIES EXPANDS SILICON PHOTONICS CAPABILITIES Silicon Valley, CA (Feb 9, 2021) - Integra Technologies, a world leader in
Webinar: Die Prep Processes and Overview
WEBINAR: DIE PREP PROCESSES AND OVERVIEW WEDNESDAY, DECEMBER 2, 2020, 1:00 P.M. PST
Upcoming Webinars From Integra Technologies
Sign up now for one of Integra's Webinars coming up this month: By request, Integra Technologies will be offering the
Webinar: Mil-Std-1580 DPA
Due to popular demand we will be presenting the webinar: Mil-Std-1580 DPA Including Copper Bond Wire PEMs AGAIN! Wednesday, Sep
INTEGRA TECHNOLOGIES NAMED TO THE 2020 INC. 5000 LIST
Inc. Magazine Unveils Its Annual List of America’s Fastest-Growing Private Companies—the Inc. 5000 Integra Technologies Ranks on the 2020
Integra Technologies Secures $20.7 Million F-35 Contract
INTEGRA TECHNOLOGIES SECURES A $20.7 MILLION CONTRACT AWARD FROM F-35 JOINT STRIKE FIGHTER PROGRAM OFFICE
INTEGRA TECHNOLOGIES SECURES A $20.7 MILLION CONTRACT AWARD FROM F-35 JOINT STRIKE FIGHTER PROGRAM OFFICE
*All contract work to be done at Integra's 250 employee Wichita facility*
WEBINAR: Obsolescence Management for EEE Parts
Join Integra, Wednesday, July 29th, at 1:00 p.m. PST to learn more about the Obsolescence Managemnet for EEE Parts
INTEGRA TECHNOLOGIES WINS $3 MILLION CONTRACT AWARD FROM NORTHROP GRUMMAN
*U.S. Senator Jerry Moran congratulates Integra, looks forward to seeing additional military related manufacturing in Wichita*
Integra Wins $3 Million Contract Award From Northrop Grumman
U.S. Senator Jerry Moran congratulates Integra, looks forward to seeing additional military related manufacturing in Wichita Wichita, KANS.
Obsolete Parts Management with Integra Technologies
Integra’s Parts Management Program (PMP) started in 1991, actively managing multiple Aerospace and Defense companies’ parts procurement
WEBINAR: Standards of PEM Qual and Technical Requirements Review
Standards of PEM Qual and Technical Requirements Review Integra is the leader in performing PEM (Plastic Encapsulated Microcircuits)
Expanded RF Services from Integra
Whatever your specific RF requirements, Integra can help. For over 35 years, Integra has been an integral part of our customers
Construction Analysis from Integra Technologies
Construction Analysis from Integra Technologies Construction Analysis gives a detailed view of the construction quality and materials used
Die Prep Services from Integra
DIE PREP SERVICES Integra Technologies Silicon Valley, previously CORWIL Technologies, specializes in ultra-thin precision wafer thinning
Case Study: Saluda Medical
CASE STUDY: Integra has been an indispensable part of Saluda Medical’s growth and ongoing successes towards commercialization of the
ISTFA - Portland, Going on Now!
Stop by Booth #203 at ISTFA at the Portland Convention Center today and tomorrow to say 'Hi' to Sultan and Mark! Let them help you with
Integra is at IMAPS Boston NOW!
Stop by booth #401 at IMAPS Boston today and tomorrow and say Hi to John and Richard. They are eager to discuss Integra Technologies'
Integra Technologies at IMAPS Today!
Visit Integra Technologies September 30 - October 3 - Boston, MA - Booth #401 As a high-performance IC packaging provider, Integra
IMAPS Advanced System and Technology Conference Follow Up
Thank you to all who visited us last week at the IMAPS Advanced System and Technology Conference. It was a great turn out and we enjoyed
Visit Us at the IMAPS Advanced System in Package Technology Conference and Exhibition June 25-27
Integra's System-in-Package & MCM solutions offer the capabilities of a complete system in one device. As a high-performance
Heterogeneous Integration Roadmap Symposium 2/21-2/22
There was a great turn out at this year's Heterogeneous Integration Roadmap Symposium in Milpitas, CA last week. We would like to thank all
MEPTEC Symposium Today!
Stop by the Integra booth today and say hello to Rafi, Chip and Richard, 9:30 - 6:30 p.m.
MEPTEC Symposium, December 5
Visit Integra Technologies at MEPTEC's 'Heterogeneous Integration' Symposium, this Wednesday, December 5th from 8:00 - 5:00 with exhibits
ISTFA Going on Now!
ISTFA is going on now at the Phoenix Convention Center. Stop by booth #731 and say Hello!
-55°C Electrical Testing from Integra
Integra Technologies uses its advanced automated test equipment (ATE) for the purpose of testing at -55°C and beyond. In support of
INTEGRA TECHNOLOGIES ANNOUNCES NEW WEBSITE LAUNCH
The new and completely redesigned website offers visitors richer insight into Integra’s compelling capabilities in die preparation,
Open House TODAY!
Stop by and say 'hello' to the Integra group - facility tour, food and drinks! 3:00-7:00 p.m.!
OPEN HOUSE - June 19th!
Join us for an Open House at our Milpitas, CA facility Tuesday, June 19th! The Open House includes facility tours, wine tasting and hors
Case Study: GaN Wafer Dicing
CHALLENGE:To develop a singulation process for GaN wafers that consistently provides high quality and yields.
GSA Silicon Summit
Visit Integra this Thursday at the GSA Silicon Summit! Stop by Booth 10 and tell Joe, Ron and Jeff hello!
Visit Integra Technologies at DMSMS 2017, Booth #920
Integra Technologiesprovides a complete portfolio of turn-key services to support Military/Space/Aerospace companies threatened with
New Signs are up!
The new signs are in place at Integra Technologies! Stop by and take a look. Thank you Cordero Printing.
Going Green
Integra Technologies Silicon Valley (formerly CORWIL Technology) has partnered with Mynt Systems to take part in helping the environment by
Over 1 Million CSPs Assembled
MILPITAS, CA, October 10, 2017 – Integra Technologies (formerly CORWIL Technology) announced today that it has successfully produced over 1
Case Study: Captive Line
Read about how CORWIL Technology provided an in-house turnkey solution for a top fabless networking company that needed to implement volume
See What CORWIL Has to Offer
In response to the requests we’ve received about our processes and types of equipment we have, CORWIL has created aYoutube Channelto show
CORWIL Adds FTI 1000 Tester - Good to 3600V and Testing of Power Devices
CORWIL Technology (CORWIL) has teamed with Focused Test, Inc. to release the FTI 1000. The FTI 1000 tester adds to a growing variety of
CORWIL's Commitment to it's Customers
When CORWIL was approached by a medical customer that had developed a product that required a very small and strong die, CORWIL
Device Test and Package Solutions for Silicon Photonics
CORWIL Technology’s pursuit of cutting edge technology and prime location in the heart of Silicon Valley has led them to secure programs
CORWIL Invests in Portable Clean Environment
To satisfy customer demand for ultra-clean environments for wafer sort, CORWIL Technology (CORWIL) has added a Portable Clean Environment
CORWIL Technology Receives Trusted Accreditation
Milpitas, CA, October 19, 2016 – CORWIL Technology (CORWIL), headquartered in Milpitas, CA, has received Trusted Accreditation by the
Medical Electronics Symposium 2016
Visit us at SMTA's Medical Electronics Symposium, September 14 & 15 at Marylhurt University in Portland, Oregon. This year's Key Note
Reliability Testing from CORWIL Technology
What's NEW... CORWIL can now perform ALL JESD22-A113 Precondition work IN-HOUSE, as well as before and after CSAM with the Sonoscan D9000.
Dice Before Grind (DBG) for Medical Devices
CORWIL was recently approached by a medical customer who had developed a tiny wearable device that included a small bare die with
CORWIL INCREASES WAFER SORT CAPABILITY
Milpitas, CA, April 27, 2016 – CORWIL Technology (CORWIL) continues to demonstrate its full turnkey capabilities for its customers by
CORWIL Technology Receives Recognition from Device Engineering Incorporated
CORWIL TECHNOLOGY RECEIVES A PERFECT SCORECARD FROM DEVICE ENGINEERING INCORPORATED Milpitas, CA, March 16, 2016 – CORWIL Technology
Processing III-V and Other Non-Silicon Materials
CORWIL Technology successfully processes a number of materials through its wafer processing facility. While Silicon is the majority of
CORWIL Technology Receives Excellent Performance Report Card from Microsemi Corporation
CORWIL Technology Receives Excellent Performance Report Card from Microsemi Corporation Milpitas, CA July 21, 2015 - CORWIL Technology
CORWIL Technology Producing Volume Plastic Parts Including MicroSD and QFN
Milpitas, CA June 18, 2015 - CORWIL Technology announced today that it has more than doubled its QFN production in 2015 and recently
CORWIL Technology Receives Quality Management System
Milpitas, CA, May 6, 2015 - CORWIL Technology announced today their Certification to the Aerospace Quality Management System, AS9100C,
CORWIL TECHNOLOGY TEST, RELIABILTY AND EOL SERVICES
Milpitas, CA, March 11, 2015 - CORWIL Technology has fully integrated Test, Reliability and EOL services along with wafer preparation and
Assembly and Test Open House Success
Thank you to all of our customers, colleagues and friends who attended our Open House on Wednesday! Visitors were able to take a tour of
CORWIL Technology Selected as Supplier of the Year by Inphi Corporation
Milpitas, CA, February 4, 2015– CORWIL Technology (CORWIL), the premier US based, IC assembly and test services subcontractor, offering
CORWIL Technology Combines Assembly and Test in One Location
Milpitas, CA, December 18, 2014 - CORWIL Technology now offers assembly and test services to their customers all under one roof. CORWIL
Die-Prep Considerations for IC Device Applications
Earlier this month, CORWIL's own Jonny Corrao, Engineering Manager, presented 'Die-Prep Considerations for IC Device Applications,' at the
INTEGRA TECHNOLOGIES SELECTED BY THE DEPARTMENT OF DEFENSE MISSILE DEFENSE AGENCY TO COMBAT COUNTERFEIT ELECTRONICS
WICHITA, KS - Oct 21, 2014 - Integra Technologies LLC, a world leader in integrated circuit test and related services, announced today that
CORWIL Focuses on MedTech Industries
CORWIL Technology is a U.S. based OSAT with a unique focus on Medical Device and Biotech industries. Our Bay Area facilities are state of
CORWIL Increases Die Attach Capacity with a New MAT 6400
Milpitas, CA, March 31, 2014 – CORWIL Technology (CORWIL) announces continued invest ment in capabilities with the addition of a new MAT
CORWIL Increases Molding Capabilities with a FICO MMS-W Molding System
CORWIL INCREASES MOLDING CAPABILITIES WITH A FICO MMS-W MOLDING SYSTEM Milpitas, CA, November 22, 2013 – CORWIL Technology announced the
Want to Learn More About Die Singulation?
Die singulation is the process of isolating individual IC’s from a wafer. There are a variety of methods for die singulation with the most
INTEGRA TECHNOLOGIES APPROVED BY DLA FOR MIL-STD-750 PROCESSING
WICHITA, KS - Oct 13, 2013 - Integra Technologies, a world leader in integrated circuit test and related services, is pleased to announce
What is Wafer Thinning?
Wafer thinning is the process of removing material from the backside of a wafer to a desired final target thickness. The two most common